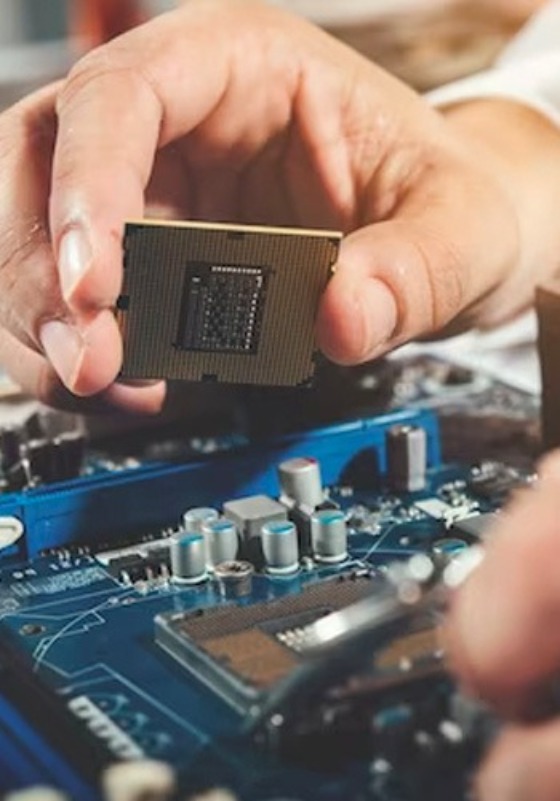
提高功率元件效能的封裝技術
對功率密度提升的需求為功率元件及其封裝與冷卻技術帶來了特定的挑戰。在電源轉換過程中,高溫和溫度波動限制了最大功率輸出、系統效能和可靠性。本文將概述兩種不同的技術手段,旨在盡可能提高電源模組和元件的熱效能與功率密度。這些方法由Littelfuse在PCIM Europe 2024會議上提出。
非隔離式晶片元件結合直接液體冷卻
半導體電源模組通常由安裝在直接銅接合(DCB)基板上的功率元件裸晶組成。對於中大功率的模組,這種基板通常是電絕緣陶瓷材料,如氧化鋁(Al2O3)、氮化矽(Si3N4)或氮化鋁(AlN)。接著,可以將基板連接到諸如銅的導熱基板上,並在其上裝配外部散熱器。寬能隙(WBG)半導體,例如碳化矽(SiC),以其更高的效率和功率密度著稱。
在模組組裝製程中已有多項技術改進,以提高其熱效能並盡可能提高功率元件的能力。這些進展包括使用燒結和擴散焊接進行裸晶貼裝,以及採用具有更佳熱效能的高效能陶瓷,如氮化矽和氮化鋁。即使採用了先進的陶瓷材料——陶瓷基板可能是造成模組熱阻的主要因素——電氣隔離所需的厚度與由此產生的熱阻之間仍存在一種既有的權衡關係。
與上述隔離模組不同,大功率盤狀元件通常採用導電冷板製造,如鋁材。透過在冷板內流通非導電液體(例如去離子水和乙二醇混合物)實現主動冷卻。由於功率元件和散熱器之間不存在絕緣層,因此提高了熱傳導效率。此概念已在矽IGBT裸晶上得到驗證,以下將進一步詳述。
設置1:內建打線接合元件的先進IGBT裸晶
在此,兩個額定值為1,200V/200A的IGBT裸晶被焊接到一塊液體冷卻板上。冷卻板充當IGBT集電極的電氣連接,而發射極和控制引腳則需透過隔離端子來實現。裸晶面積約為200mm2,採用了能夠使得在額定電流為200A時正向電壓僅為1.2V的先進設計。這種新設計還將退飽和電流與額定電流之比提升至超過6倍,從而實現了超過600W/cm2的高功耗密度(當電流達到650A且正向壓降為2V時,200mm2的裸晶總功耗可達1,300W)。
每個裸晶利用8根承載能力達25A的接合線將其發射極連接到電源端子。為了進行熱測量,裸晶表面被塗黑。實驗採用了大電流低電壓電源為裸晶供電,電流逐步遞增,每次增量為50A,直至裸晶結溫達到允許的最大值150℃。圖1展示了冷卻板上裝配好的裸晶及其在200A電流條件下拍攝的熱影像。
圖1:安裝於冷卻板上的IGBT裸晶及其頂部打線接合,以及在200A電流條件下拍攝的裸晶熱影像。(來源:Littelfuse)
在此配置下,接合線將最大電流限制在250A,在該電流強度下接合線熔斷。在額定電流為200A的情況下,裸晶溫度僅上升70K,說明熱阻小於0.1K/W,這凸顯了裸晶及其元件出色的熱管理效能。
設置2:帶有夾片元件的IGBT裸晶
為了解決上述設置中接合線帶來的局限,本研究採用了一種可焊接正面金屬化的IGBT裸晶,實現了夾片頂部裝配並在IGBT正面設置了介面焊盤金屬層。這種183mm2的裸晶額定值為12,00V/150A,並未採用設置1所示裸晶所具有的先進低正向電壓設計。圖2展示了裝配完成後的裸晶及其在200A電流條件下的熱影像,從中可見,接合線的限制已被克服。在此配置中,裸晶所能承受的最高功耗密度為380W/cm2。同樣,即便是在以150A額定電流的元件驅動200A電流的情況下,結溫仍遠低於允許的175℃極限。
圖2:安裝在冷卻板上的IGBT裸晶及其頂部夾片接合,以及在200A電流條件下拍攝的裸晶熱影像。(來源:Littelfuse)
在研究過程中,對設置2進行了功率循環(PC)測試。測試期間,入口溫度設定為12℃,透過實施4秒週期、工作週期50%,以及負載電流250A的操作,實現了90K的晶片溫度變化幅度。根據圖3所示的結果,依照正向電壓增加5%的標準評估,使用壽命達到了145,000個週期。隨著晶片金屬化處理、焊料合金和焊接製程的持續改進,預期壽命可望進一步延長。
圖3:功率循環測試結果。(來源:Littelfuse)
應用領域
上述非隔離式模組適用於多種大功率應用場景,例如風力渦輪機中的再生能源發電、鋼鐵工業中的金屬冶煉或感應加熱焊接、電池斷路開關及斷路器。整合液體冷卻不僅能夠提高功率元件、端子和直流母線電容器等各類系統元件的可靠性和使用壽命,而且由於工作溫度降低還能簡化外殼的設計。
隔離式TO-247封裝:ISO247
ISOPLUS是IXYS (目前隸屬於Littelfuse)於2003年首次在氧化鋁基板上開發的一系列內部隔離離散式功率元件封裝。作為ISOPLUS家族成員之一,ISO247與標準TO-247封裝引腳相容。ISO247的核心理念在於在為裸露的汲極焊盤提供既有的電氣隔離的同時,保持從裸晶到該焊盤的高效熱傳導路徑。相較之下,傳統的TO-247在連接至散熱器時需要外部隔離措施,為此常會用到電氣絕緣的導熱箔片。然而,這樣做可能會顯著增加元件的結至散熱器的熱阻,進而嚴重影響元件的最佳效能和功率容量,尤其是對於像SiC這樣的WBG元件而言,因為大功率往往是這類系統的首要需求。
本研究中使用的ISO247封裝經過了改良,以滿足如SiC MOSFET等大功率元件的要求。其中包括:
.使用Si3N4陶瓷基板:它擁有約90W/mK的高熱導率,以及約2.4ppm/K的低熱膨脹係數,這與半導體裸晶的熱膨脹係數相近。高電氣隔離度加上良好的機械效能使其成為高功率密度應用的理想選擇。本研究中使用的ISO247封裝具有2.5kV交流電持續1分鐘或3kV交流電持續1秒的隔離等級。
.混合活性金屬釺焊(H-AMB)技術用於基板的金屬化處理:這一過程包括使用活性金屬填充層的初始濺射製程,隨後在約850℃的溫度下將銅釺焊到濺射表面上。這種H-AMB製程確保了出色的熱傳到效果、成本效益,以及無氣孔的接合表面。
ISO247和TO-247封裝之間的結構和安裝差異,如圖4所示。
圖4:ISO247和TO-247兩種封裝的內部結構及安裝差異。(來源:Littelfuse)
SiC MOSFET熱效能對比
針對1,200V、25mΩ SiC MOSFET裸晶,分別對其在ISO247和TO-247封裝下的熱效能進行比較。TO-247外殼分別搭配了熱導率為1.8W/mK和6.5W/mK的外部隔離箔。ISO247封裝則在隔離漏極焊盤和散熱器之間塗抹了導熱膏。所有元件均安裝在水冷散熱器上,並維持恆定的30℃環境溫度。
當加熱電流為40A時,所得的熱阻(RthJH)和結溫(Tvj)數據,如圖5所示。
圖5:ISO247和TO-247兩種封裝的熱阻抗及結溫資料。(來源:Littelfuse)
結果顯示,ISO247封裝的RthJH比配備更高熱導率導熱箔的TO-247降低了55%,並且在同一元件功率和外部冷卻條件下,從裸晶到散熱器的溫度差也減少了39%。由於熱機械應力的降低,這些指標的改善可直接提高可靠性;同時,鑒於元件功耗和漏電流通常在較高溫度下會增加,這些指標的改善也有助於提升效能。
利用ISO247提高功率輸出或降低晶片成本
上述獲得的熱資料還可以用來估算在給定最高結溫下元件可增加的功率容量。研究發現,與TO-247相比,ISO247能夠在相同的130℃晶片溫度下傳導高出30%的電流,從而充分發揮SiC的效能。對於一個直流母線電壓為800V的主動前端轉換器而言,透過使用熱導率更高的導熱箔,ISO247可將TO-247原本的22.7kW功率容量提升至約30kW,如圖6所示。另一種利用ISO247熱效能改善的方法是在保持與TO-247相同額定功率的條件下,選用具有更高導通電阻(RDS(on))的裸晶,以此來節約裸晶成本。
圖6:採用ISO247封裝後估計可增加的應用功率輸出。(來源:Littelfuse)
(本文已獲得授權轉載,原出處為 EE Times Taiwan: 提高功率元件效能的封裝技術)
(參考原文:Packaging Techniques for Improved Power Device Performance,by Sonu Daryanani)